TECHNOLOGY
Esperança invests considerably in technological innovations aligned with time and new market resources, offering reliable products with a high quality standard.
Through simulation software such as Defom and eesy2-Form, tensions and countless other factors from the forming process are analyzed. Such resources guarantee a better performance of the tools during the process and allow a thorough analysis of the material's behavior. The entire tooling and process design is developed using CAD, 2D and 3D tools, such as AutoCad Mechanical and Inventor. The results are products of superior quality, cost optimization and resources that directly and considerably influence the final cost of the part.

RELIABLE AND PRODUCTIVE PROCESS

The parts offered meet the most diverse applications and requirements, through a manufacturing process with very high precision, thus excluding time-consuming and costly control operations. Each item is analyzed in a unique way and in particular, with production availability on automatic machines and compatible and necessary resources. With the reduction or elimination of machining, the production cycle of the parts is also reduced, optimizing the storage space between processes and shipping. In special cases, welded assemblies can be replaced, with enormous savings and improved quality, by a single cold forged part.
DEVELOPMENT AND FLEXIBLE DESIGN
In order to guarantee the most viable solution to the client's project, Esperança has an Engineering Department with the most modern simulation and development equipment ensuring that they meet all the parameters and specifications required by the client. Thus, it offers a Flexible Project making the necessary adaptations to the customer's project and the cold forging process, always aiming at maximizing production, reducing costs and deadlines.
All specifications are thoroughly analyzed in order to elaborate projects aiming not only to increase the tool's useful life, but also to decrease the final cost of the part.
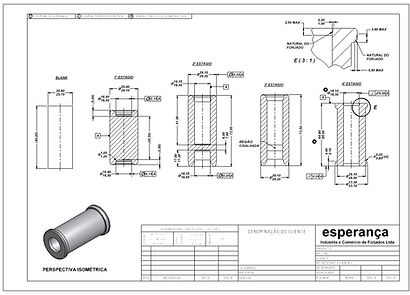
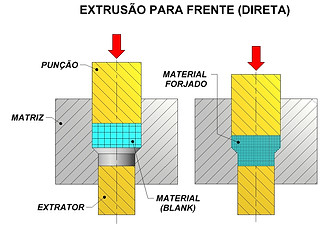
COLD FORGING
Cold forging is a plastic deformation of metals, at room temperature, where the material is forced by compression to flow between a die and a punch, thus allowing the manufacture of components with great dimensional precision, complex geometries and finishing close to the use of the part . It is a forming process where there is no material removal. In this way, cold forged products are hardened, with a high level of mechanical resistance.


CHARACTERISTICS
This technology has already proven to be highly economical and efficient. Its applications are growing rapidly thanks to its potential in the development of parts with more complex geometric shapes, manufactured with raw materials that allow a greater degree of deformation.


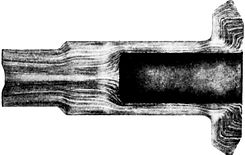
FIBERING AND CROSSING
Because it is a process that moves the material without removing it, there is a movement of the fibers along the formed part, without interruptions or cuts. The result is an exceptional gain in mechanical properties, such as increased fatigue and shock resistance. It is also possible, in some cases, to eliminate heat treatments after the forging process.
ECONOMY
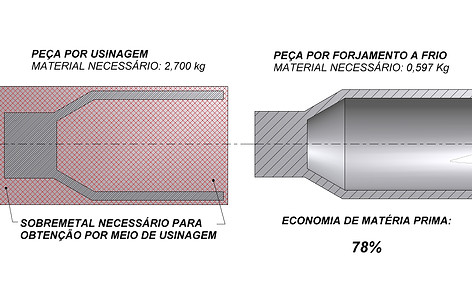
Because they have good dimensional stability, cold forged parts require little or no finishing machining, thus saving material and machining labor. The economy becomes a great differential since there is no loss of material.
This point also becomes relevant in situations where higher cost materials are used, such as aluminum and its alloys.

FEEDSTOCK
Non-ferrous materials such as lead, zinc and copper were the first applications of cold forging. The hardening effect that causes an increase in mechanical strength was extremely relevant and adopted as a differential for the process. The materials most used in the process are steels that have less alloys in their constitution because they offer less resistance to deformation.
Among these materials, we can highlight:
> Low carbon steels (up to 0.45% C)
> Low alloy steels (SAE 1524, 4130, 5135, 8620, among others)
> Aluminum (ASTM 1100, 1200, 2014, 6061, among others)
> Copper (B102, B110, B145)
PRECISION FINISHING
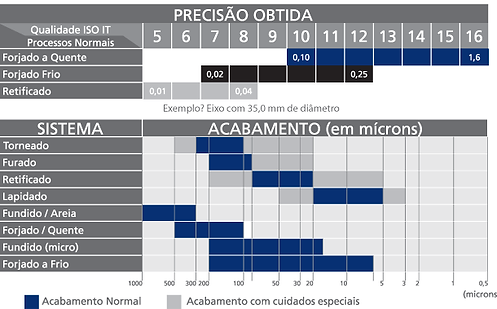
We can observe that cold deformation can generate parts with excellent finish and great dimensional precision, with a tolerance of ± 0.10 mm, thus reducing material, time and labor to obtain the finished part.
Check the accuracy and finish by consulting the comparative tables between the different production processes:

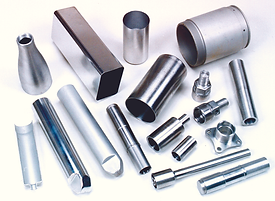
SHAPES
With suitable designs, we can produce parts whose manufacture, by other methods, becomes more difficult or impractical. Cold forging is the most practical solution on the market.
MEASURES FOR PARTS PRODUCTION


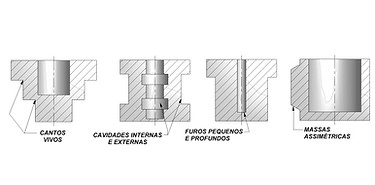

IMPROPER PROFILES
Parts that have sharp corners, internal recesses, holes with small and deep diameters, as well as asymmetrical masses, are not suitable for the cold forming process.
Parts with sudden variations in dimensions, such as those with asymmetric profiles and masses, become economically unfeasible if obtained through the cold forging process.